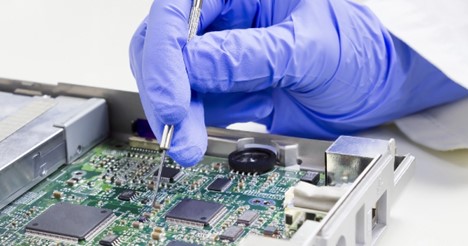
From PCB to Product – Understanding the Box Build Process
The journey from a PCB prototype to a fully functional product is complex yet critical. While many discussions focus on the PCB itself, the final product often depends on a well-orchestrated assembly process known as the box build. This process integrates the PCB with all the mechanical, electrical, and even software components into a complete, ready-to-use unit.
Sonic Manufacturing provides these integration services to support today’s business models. We work with both standard and custom-designed enclosures as part of our turnkey solution. Let’s break down the box build process step by step and explain how each phase contributes to creating a high-quality end product.
What Is a Box Build?
A box build refers to the complete assembly of a product, which starts with a printed circuit board and extends to include all associated components—such as enclosures, connectors, cables, and even firmware. Essentially, it’s the transformation of individual parts into a cohesive, fully functional system. This process is vital for products ranging from consumer electronics to industrial equipment, ensuring that all components work seamlessly together.
Key Steps in the Box Build Process
PCB Fabrication and Assembly
The journey begins with PCB fabrication, where the board is manufactured according to the design specifications. This stage involves etching the circuit patterns onto a substrate and applying solder masks and silkscreens.
Once the board is fabricated, automated pick-and-place machines position components with high precision, followed by soldering processes like reflow or wave soldering to secure the components in place. Automated Optical Inspection (AOI) and other testing methods help ensure that the board meets quality standards.
Sub-Assembly Integration
After the PCB is complete, connectors, cables, and other subassemblies are added. This might involve manual assembly or further automation to integrate components that require special handling. For many products, the integration of firmware or pre-loaded software is a critical step. This ensures that once the product is fully assembled, it’s ready to function out-of-the-box.
Enclosure and Mechanical Assembly
The enclosure not only protects the PCB and internal components but also plays a major role in the product’s usability and aesthetics. It’s designed with considerations for heat dissipation, ergonomics, and overall durability.
This phase also involves the physical assembly of the enclosure around the PCB and its subassemblies. It may include fastening screws, adhesives, or snap-fit designs that secure the internal components while allowing for maintenance.
Final Testing and Quality Assurance
Before the product leaves the factory, rigorous testing is performed to ensure that all integrated systems work together as intended. This can include electrical testing, mechanical stress tests, and environmental simulations. Comprehensive inspections also verify that the final product meets all specifications and regulatory standards.
Best Practices for a Successful Box Build Process
- Integrated Design Approach. Early collaboration between design, manufacturing, and quality assurance teams can help prevent integration issues. Designing with the box build in mind ensures that the PCB and enclosure work together harmoniously.
- Automation Where Feasible. Implementing automation not only increases production speed but also enhances consistency and quality. From PCB assembly to final testing, automation can reduce human error and lower production costs.
- Robust Testing Protocols. Incorporate testing at multiple stages to catch issues early. In-line inspections during PCB assembly and comprehensive end-of-line testing help maintain high-quality standards.
- Feedback and Continuous Improvement. Use data gathered during the box build process to identify bottlenecks and areas for improvement. Continuous refinement ensures that the process evolves with technological advances and market demands.
Box Build Assembly Services
The box build process is the critical link between a functional PCB and a fully realized product. By understanding and optimizing each step, manufacturers like Sonic Manufacturing can deliver products that meet technical specifications and excel in quality and reliability. For customers and end users, this means receiving a well-integrated, ready-to-use product that performs consistently. To request your free quote or learn more about our box build process, contact Sonic at 510-822-6644.