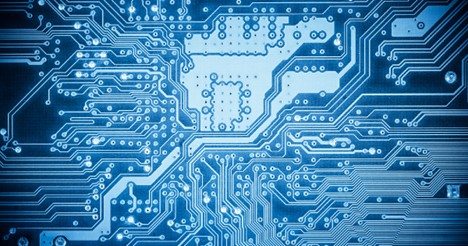
Future Trends for Printed Circuit Boards – What Lies Ahead
From the advent of single-layer boards to today’s cutting-edge, high-density interconnect (HDI) designs, the evolution of printed circuit boards (PCBs) has been relentless. As consumer demands escalate and industries pivot toward new technologies, PCB manufacturing must remain at the forefront of innovation. Here’s an in-depth look at the major trends shaping the future of PCB design and production—from novel materials and form factors to next-level design tools and sustainability concerns.
Miniaturization and High-Density Interconnect (HDI)
Electronics keep shrinking, yet are expected to do more. Devices like smartphones, wearables, and the countless IoT sensors found in our homes, workplaces, and cities all demand compact form factors with advanced functionality. This ongoing push drives PCB designers to pack as many components as possible within tighter dimensions.
High-density PCBs allow more processing power in less space. They’re essential for everything from cutting-edge mobile devices and wearables to advanced medical implants and beyond. Other advancements include stacked and staggered vias to reduce layer counts without compromising routing possibilities and embedded components, which involve placing passive and even active components inside inner layers to save space.
Flexible, Rigid-Flex, and Stretchable PCBs
Electronics no longer need to stick to rigid form factors. Flexible and stretchable PCBs are swiftly moving from niche applications—like foldable smartphones and medical patches—to mainstream solutions, thanks to breakthroughs in substrate materials and manufacturing techniques.
Flex-rigid hybrid designs integrate flexible areas with rigid sections to create devices that can bend without compromising component stability. Stretchable circuits use ultra-elastic substrates to accommodate bending, folding, and twisting. As technology weaves deeper into our daily lives—through portable devices, clothing, and smart surfaces—flexible and stretchable PCBs will facilitate entirely new product categories and user experiences.
Advanced Substrate Materials
Legacy materials (like FR-4) have been the mainstay of PCB manufacturing for decades. However, growing needs for high-frequency applications, improved heat management, and extreme reliability are driving the adoption of new substrates.
For instance, ceramic PCBs are used in high-power or high-frequency applications, offering low thermal expansion and excellent heat dissipation. PTFE (Teflon) laminates are ideal for high-frequency RF/microwave circuits used in telecommunications and radar systems. And, metal-core PCBs embed aluminum or copper layers to dissipate heat in power electronics and LED lighting. Next-gen devices will require substrates that can handle higher data rates, extreme temperatures, and stringent reliability targets.
Embedded Passives and Integrated Components
In the quest to save board space and minimize assembly costs, many designers are turning to embedded passives—resistors, capacitors, or inductors placed within the PCB layers themselves. In some advanced use cases, even active components are partially integrated or embedded.
Applying resistor films directly onto inner layers improves consistency and reduces parasitic effects. Embedding decoupling capacitors close to ICs improves power integrity, while integrated modules can combine multiple functionalities (Bluetooth, WiFi) into small, ready-to-use PCB subassemblies. The benefit in embedding components is that it can significantly reduce a PCBs footprint, enhance signal integrity, and cut assembly steps.
Sustainability and Eco-Friendly PCB Manufacturing
Environmental responsibility is becoming a top priority for both regulatory bodies and consumers. PCB manufacturers and designers are responding by exploring greener materials and processes, as well as more efficient recycling and end-of-life strategies.
In an effort to be more environmentally friendly, PCB manufacturers are increasingly phasing out hazardous substances like lead, mercury, and certain brominated flame retardants. They are also researching cellulose-based and other eco-friendly materials that break down more easily, as well as utilizing copper, gold, and other metals from discarded boards.
AI-Powered Design Tools and Industry 4.0 Integration
Manual PCB layout can be time-consuming and prone to human error, particularly for advanced or high-speed designs. Increasingly, AI-driven EDA (electronic design automation) tools are taking over complex routing and optimization tasks. Simultaneously, production lines are becoming more digitized, leveraging real-time data and automation for quality control and efficiency.
Key advancements include AI-assisted solutions that optimize trace paths, digital twins (virtual replicas of the manufacturing process), and data integration using advanced MES (manufacturing execution systems). By reducing design cycle times and production risks, AI and Industry 4.0 automation enable faster innovation and more cost-effective manufacturing.
Conclusion
Printed circuit boards may not always attract the same hype as the latest smartphone or electric vehicle, but they are the essential backbone driving today’s technological breakthroughs. From miniaturization and flex-rigid designs to 3D printing, high-speed data handling, and sustainability, the future of PCBs promises innovations that will reshape product design, manufacturing, and the entire electronics industry. To get a free quote for your PCB project, contact Sonic Manufacturing Technologies today.